What to know when selecting and installing concrete fastener in an industrial application. First, know the requirements of the application.
Contractors can improve the results of their industrial projects by learning more about the types of concrete fasteners that are available. It is important to select a fastener based on the specific requirements of the application. In addition, learning how to properly install the fasteners is crucial to ensure long term safety and stability. Stainless Steel Pipe Anchor
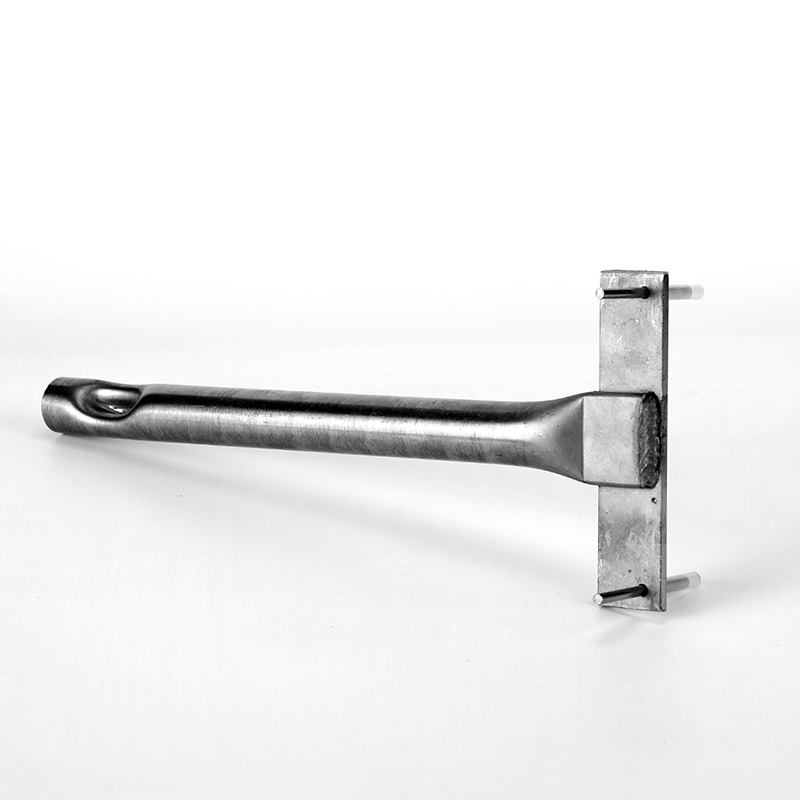
According to OSHA Regulation 1910.212(b), machines designed for a fixed location shall be securely anchored to prevent walking or moving. Therefore, it is important to consult the manufacturer’s specific anchoring instructions. Wedge anchors are typically used to secure machinery to concrete floors and walls as they provide the highest and most consistent holding values compared to other mechanical expansion anchors.
Concrete Fastening Systems, Inc. Wedge Anchor Technical Specifications - Wedge anchors are available in a variety of lengths and diameters, selecting the proper size is key to safe and secure installations. They also come in various finishes depending on the environment in which they are used. For example, zinc-plated anchors are sufficient for most dry applications. Galvanized and stainless-steel anchors are used in environments that are wet or exposed to moisture.
To determine the length of wedge anchor required, add the thickness of the material to be fastened, plus minimum embedment, plus the thickness of the nut and washer. The sum of these three items equals the minimum wedge anchor length. The hole depth in the base material should be at least the anchor's length minus the fastened material's thickness. Provide some extra depth to accommodate some space for concrete dust that cannot be removed from the hole.
Spacing - The forces on a wedge anchor are transferred to the base material in which it is installed. If anchors are installed too close together, an interaction of the forces might reduce the anchor's holding power. The expansion anchor industry has established a minimum standard of ten anchor diameters for spacing between anchors and five anchor diameters from an unsupported edge. When vibration or sudden impact is part of the load conditions, the spacing between anchors should be increased.
Watch the installation of concrete wedge anchors.
Pallet racks are essential for many industrial and commercial facilities. Regardless of the facility, all racks must be anchored for stability and security.
After the facility racking floor plan is designed and the racks are assembled, it is critical to ensure that all the racks are level before installing any anchors or screws. It is also essential to ensure that every column of the rack frame will be anchored to an adequate and stable concrete floor. Deciding which anchor to use is typically based on the manufacturer's recommendation or personal preference.
Tip: A vertical tolerance of 1/8 in. in 4 ft. is generally accepted as level in most applications.
Large Diameter Hex Head Concrete Screws - Some contractors choose to use hex head large diameter concrete screws when installing pallet racks and other structures. It is recommended to use high-quality concrete screws specifically designed for heavy-duty applications, such as pallet racks, ensuring a secure and long-lasting installation that can withstand the weight of the pallet racks and their contents.
Drop-In Anchors for Electrical Trapeze or Ductwork - The cement drop-in anchor is primarily used with a threaded rod for installations in ceilings for hanging electrical trapeze, ductwork, or other mechanical apparatus. The cement drop-in anchor is a flush-mounted anchor used in conjunction with standard bolts that allows for attaching and removing if necessary.
Cement drop-in anchors have a female thread, and are designed for solid concrete, they cannot be used in brick or block base material. The drop-in cement anchor comes in five diameters 1/4, 3/8, 1/2, 5/8, and 3/4 in., with each diameter available in only one length.
The drop-in anchor requires the use of a setting tool to set the anchor into the cement. Once the cement drop-in anchor is set, the contractor can insert a bolt or threaded rod and remove it as often as required.
Watch the installation of drop-in anchors.
Concrete Fastening Systems, Inc. Head Styles - Masonry screw anchors are available in two different head styles for various applications. Flat head countersunk Phillips screws can be used where a flush finish is required. If the material being installed is not able to be countersunk, then a hex head washer screw should be used.
Material - Masonry screws are manufactured from carbon steel, which has a blue coating, or from 410 stainless steel.
The standard, blue-coated masonry screw is used in indoor applications where moisture is absent.
For outdoor use or in moist environments, 410 stainless-steel should be used.
Tapping Process - Masonry screws typically cut their own threads into the base material and are designed to cut threads up to 1-3/4" in depth. The abrasiveness of the masonry will determine the exact depth that any specific screw can tap. The lead thread will dull and hit a point where it will no longer be able to cut threads.
As the threads are cut into the masonry, dust is created. The threads are designed to remove the dust and prevent interference with the screw installation. Therefore, the hole drilled in the masonry must be slightly deeper than the length of screw to allow space for the dust to fall into and out of the way.
Diameter of Hole - The hole diameter is critical and must be drilled following the manufacturer's instructions. The guidelines for masonry screw anchors are as follows: the 3/16-in. diameter requires the hole diameter to equal 5/32-in., and the 1/4-in. diameter requires a 3/16-in. hole. The hole must be drilled using a carbide drill bit that meets ANSI standards. Any variance in hole size will affect the holding values and may make the hole unusable.
Making the Hole - The hole in the masonry must be drilled using an ANSI standard carbide tipped bit used in a hammer drill. Set the drill to hammer and rotation mode to ensure that the hole is in the proper condition to allow the screw to obtain minimum holding values. Once the hole is drilled, all dust and debris must be cleaned, or holding values may be affected. Using a wire brush, compressed air, or vacuum in combination is usually sufficient to clean out the hole before inserting the screw.

Wall Hanging Bracket This has been a brief overview of some of the available concrete fasteners and their applications. Always contact your concrete supplier and equipment manufacturer for additional information concerning the proper anchors and installation for your application.